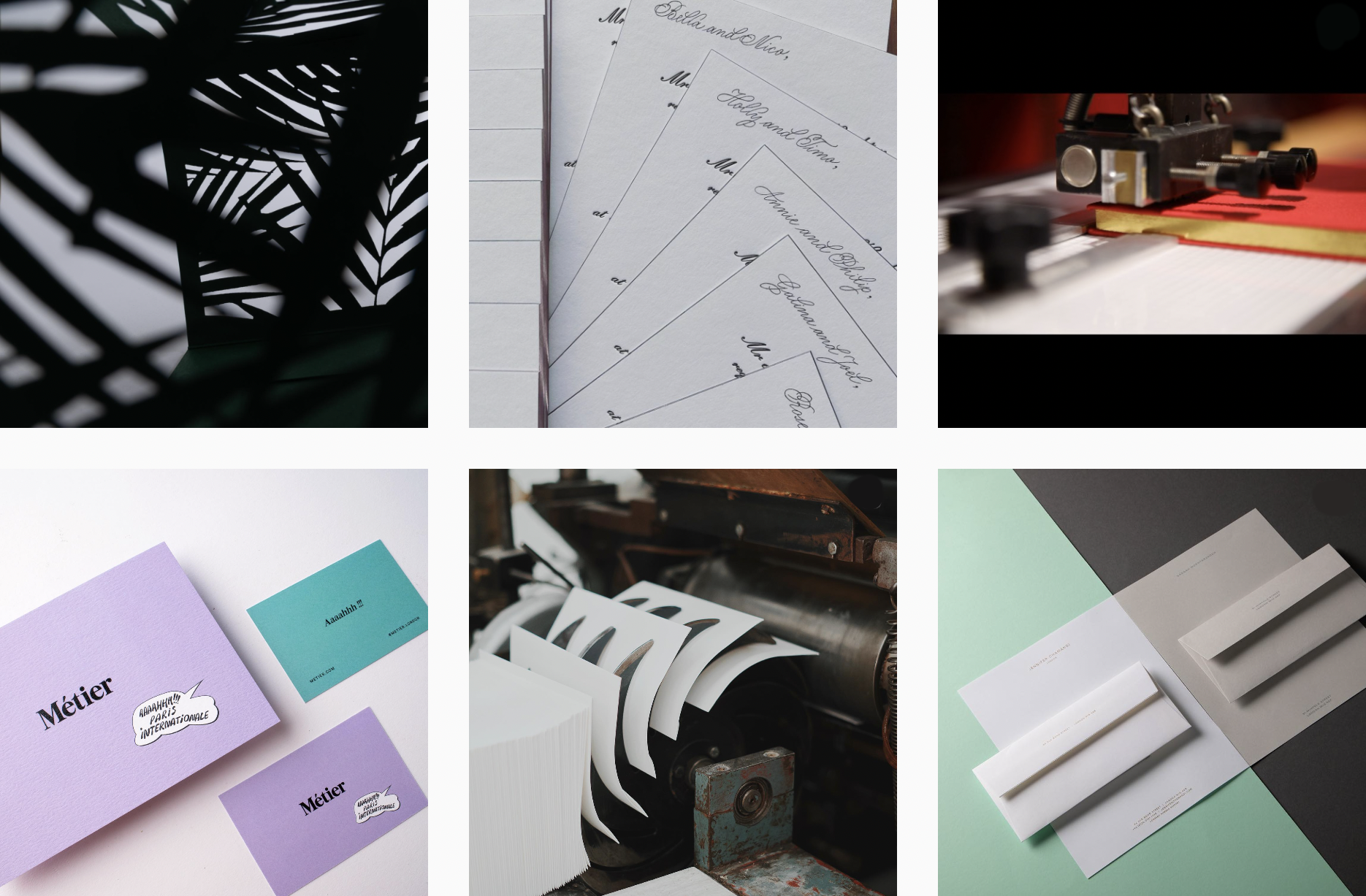
Specialty printing shops are special, indeed. Far from digital printing (where everything is generated in one tidy machine), specialty printing comprises one and two-color offset lithography, letterpress, embossing, die-cutting, and folding, as well as bindery work and (best of all) engraving, not the kind you find in random craft shops, but genuine commercial endeavors in which the bottom line is as important as the quality.
These kinds of shops once flourished, yet sadly, few still remain. Together, the advent of desktop publishing, digital printing, and social media proved a death knell for specialty printers, especially in the United States. In the engraving trade alone, annual sales of new engraving presses to American printing companies dropped by more than half in the 1990s, and has continued to fall, precipitously, in recent years.
And so it is with great excitement that I share this conversation with one of the principals of Mount Street Printers in London, who I had the opportunity to interview earlier this month, and who proved beyond generous in taking the time to provide answers to my queries.
Nancy Sharon Collins: Can you tell our readers a little about yourself?
Alex Cain: My name is Alex Cain. I am 45 years old, and I am the director at Mount Street Printers in London, working between our production facility and our retail space and studio. I love what I do. I am also a husband, and the father of two girls.
NSC: How did the company begin?
AC: The brand was born in 1981, the year my parents, Peter and Fridette, discovered the shop on Mount Street. The Queen’s stationers, Henningham & Hollis had previously occupied the premises, so the building has been a printers since the day it was built (1890 or thereabouts, I believe).*
NSC: Were you all trained as printers?
AC: I grew up in the shop from the age of five, and eventually joined my parents in the business full-time—after university—but of course I had always worked during the holidays, to lend a hand and in turn, to learn the ropes.
My parents had never trained in printing, but they saw a good opportunity and took a chance, learning everything from scratch and starting initially with only two employees.
NSC: Someone once told me that the Royal Academy—or another august London educational institution—taught steel die engraving, crests and seals and monograms and cyphers and the like. Are there trade schools for printing still in England?
AC: The only technical college I am aware of in the UK that teaches print is the LCC—The London College of Communication— and while they have a great print department, they don’t teach engraving. However, we have an intern at the moment who has been learning how to engrave in a Parisian college. When she reached out to ask for the internship, I had to double-check to make sure we were talking about the same process! Naturally, we encouraged her to come over and learn. We tend to encourage all kinds of apprenticeships here, so that we can preserve traditional methods of printing, to give anyone interested in print a chance to see if it’s really for them before they jump in as it is a long-term career path. We’ve all been so pleased to see a new generation of engravers—with real enthusiasm—starting to trickle through into the trade.
NSC: Who are your customers? Do you work with individuals, printing personal stationery? Or do you primarily work with larger commercial entities?
AC: A broad mix of all of the above, really: we work with anyone interested in bespoke specialist print processes, as this is not a mainstream industry like the general print business. Those who come to us generally know what they want to produce, either because they work for luxury brands, or because they’re looking for a quality product for a special event, which could be personal or commercial. We are currently taking on much more commercial work (and longer run lengths) now that our production capabilities have expanded outside of the shop and into our West London state-of-the-art production site.
NSC: I recently saw a quote in The London Encyclopaedia: “Mount Street was one of the original shopping streets when Mayfair was built”. Is the Mount Street location important?
AC: I think, for us, the location of the shop is hugely important, and key to the experience, as it differentiates us from our competitors. The shop makes us more approachable, which is important especially when working with such a tactile product. It is much easier when you can meet your customers face-to-face, to show them examples of our work, all in the comfort of a central London showroom. In addition, once a brief is finalized, clients are able to work directly on their projects with our designers in the studio (which is located at the back of the store) and we have a meeting space where we can all browse materials for each project. We also have a commercial ‘showspace’ in the basement of the shop, and have collaborated with GF Smith, Fedrigoni and Foilco each of whom have a large number of their material samples on hand. Here, we engage with design agencies and commercial customers who are looking to use specialist materials to create unique projects, or to simply browse through what is available to them.
NSC: What kinds of printing and finishing services does MSP offer?
AC: We offer a lot of processes with a focus on offset litho (mostly spot color work), letterpress, digital printing, foiling, die-cutting, laser cutting, envelope-making and of course, engraving. For some processes we can work up to B2 size and in particular, letterpress and foil, which is quite rare to find all under one roof.
NSC: I’ve seen videos on Instagram of various processes and machines in the shop, and there’s one in particular that intrigues me. What’s the back story on this impressive piece of equipment?
AC: We recently moved into envelope-making, which is normally a business in itself, but due to the high volume of envelopes that we sell—and the range of sizes and colors—it made sense to bring this in-house. It also gives us complete control over the quality of the finished product.
NSC: Preparing art for specialty printing is a fascination with me. Maybe we can use one or two of your Christmas cards as case studies. I have two favorite cards in this season’s offerings.
AC: Happy to expand on this if you tell me which.
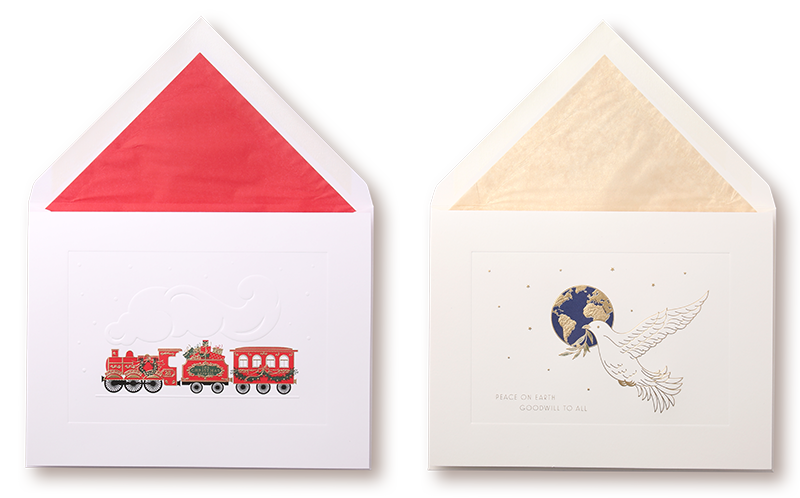
LEFT: The Christmas express Christmas card. RIGHT: Tidings of peace and joy Christmas card.
AC: The cards are usually made from a combination of print processes: for example, the first card has been litho printed in three spot colors, then engraved—in gold—with a burnish, and finally finished with a blind emboss and plate sink border. ** The second card is slightly simpler in process, with a focus on engraving and blind embossing, framed with a plate sink border. However, there is more detail in the engraving and the die has been hand-finished to give it a more sculptured appearance.
NSC: We recently came upon this curious reference that speaks to the endearing relationship you seem to have with (some of) your equipment at Mount Street Printers, and I was delighted to learn that some of your machines even have names: I’m referring here to your die-stamping machines, and in particular, to Bertha, Mildred, Gladys, and Ebony. Would you care to tell our readers about this quant custom?
AC: Years ago when we got into engraving it was almost impossible to find a machine yet alone someone to show you how to operate it. The names came from my mother as she was sentimental about these previous machines and each one is unique in having its own character!
Today we have so many machines that we dropped that tradition but the old presses retain their given names and are still running nearly 40 years after we acquired them despite some of them approaching 100 years old.
NSC: Thank you, Alex, for taking time to answer my questions. If there’s a run on your shop from Design Observer readers this Christmas, it will be easy to understand why!
* Editor’s Note. Henningham & Hollis originally took up residence in Mayfair in 1899.
** Plate sinking is debossing.